Vakuumguss: Vom Prototyp zur Form zur Kleinserie – schnell und kostengünstig
Vakuumgießen ist eines der am häufigsten eingesetzten Verfahren zur schnellen und kostengünstigen Vervielfältigung von Urmodellen und Prototypen. Dabei handelt es sich beim Vakuumguss um ein Folgeverfahren, bei der eine Silikonform aus dem Urmodell (dieses Urmodell lässt sich zeitsparend mit z.B. SLA realisieren) hergestellt wird. Diese Silikonform wiederum dient der schnellen und kostengünstigen Vervielfältigung von Kunststoffteilen in Kleinserie.
Vakuumguss kommt vor allem im Prototypenbau sowie in der Fertigung von Pilot-, Test- und Vorserien zum Einsatz. Auch Kleinserien von Artikeln mit begrenztem Marktvolumen werden mit Hilfe dieses Verfahrens hergestellt. Design-Prototypen mit hauptsächlich optischen Anforderungen dienen hierbei meist Ergonomie- und Marktstudien sowie als Marketing- und Messe-Muster. Aber auch technische Prototypen für Konstruktions-, Funktions- und Montagetests können vakuumgegossen werden.
In Serie gefertigte Vakuumgussteile sind vor allem im Automobilbau, im Flugzeugbau, in der Medizintechnik und in der Lebensmittelindustrie zu finden. Typische Vakuumgussteile sind dabei unter anderem Gehäuse, Abdeckungen und Verkleidungen, Dichtungen aller Art, Schläuche, Formrohre und Modelle, aber auch transparente Formteile wie Displays oder lichtdurchlässige Behälter.
Wichtig: Test- und Vorserien von Bau- und Formteilen müssen in ihren Gebrauchseigenschaften und ihrer Belastbarkeit möglichst weitgehend dem Endprodukt entsprechen, damit verlässliche Aussagen aus einer Testreihe getroffen werden können. Der Vakuumguss mit Silikonformen ist in der Materialauswahl zwar begrenzt. Mit modernen Gießharzen lassen sich jedoch die Eigenschaften zahlreicher Kunststoffe – Polyethylen, Polypropylen, ABS, Polyamid, Polycarbonat und anderer mehr – weitgehend abbilden, dass Funktions- und Produkttests aussagekräftige Ergebnisse liefern.
Und der Vakuumguss ist dabei erheblich schneller und kostengünstiger als herkömmliche Kunststoffspritzgussverfahren in Aluminium- oder gar Stahlformen. Eventuelle Konstruktionsänderungen oder Designanpassungen lassen sich ähnlich schnell wie bei additiven Fertigungsverfahren umsetzen. Einem Zeitraum von wenigen Tagen bis Wochen vom Prototyp zur fertigen Form im Vakuumguss steht daher ein Entwicklungsprozess von mehreren Monaten im konventionellen Kunststoffspritzguss gegenüber – mit entsprechend großen Kostenvorteilen.
Vakuumguss für Ihr Projekt gesucht?
Sie möchten prüfen, ob sich Vakuumguss als Fertigungsverfahren für Ihr Produkt eignet? Wir übermitteln Ihnen ein passendes Angebot – inklusiv Machbarkeitsanalyse, kostenlos und unverbindlich.
Das Vakuumgussverfahren: Mit derselben Methode zu Form und Werkstück
Da es sich beim Vakuumguss um ein Folgeverfahren handelt – im Prinzip ist Vakuumgießen eine Kopiertechnik –, wird immer ein Urmodell benötigt. Meist kommt hierbei ein Stereolithographie-Prototyp des zu fertigenden Werkstücks zum Einsatz. Aber auch lasergesinterte Master (vgl. Selektives Lasersintern/SLS) oder traditionell gefräste und gedrehte Prototypen finden Verwendung. Wichtig: Die Oberfläche diese Urmodells wird so aufbereitet, dass sie möglichst weitgehend dem zu fertigenden Endprodukt entspricht.
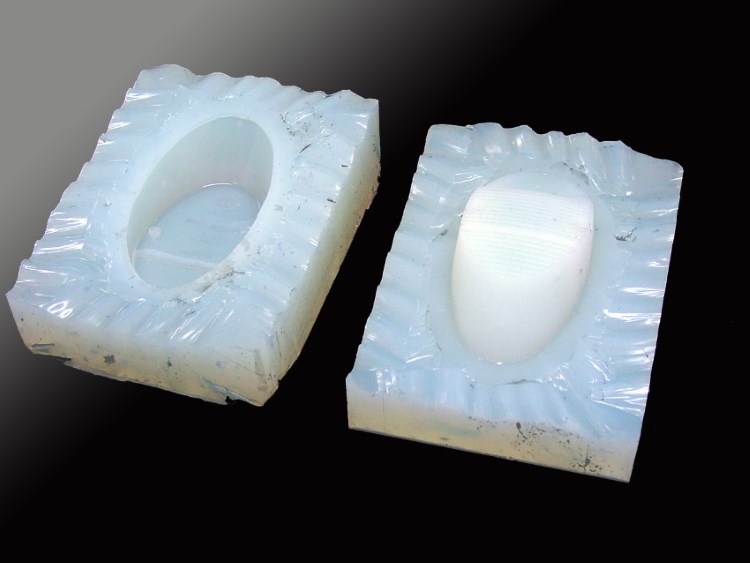
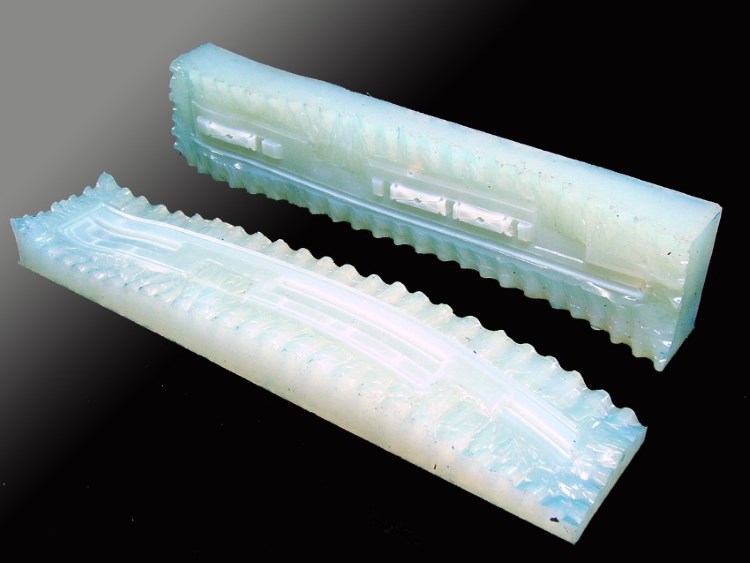
Herstellung der Silikonform: Der Prototyp wird in einer Baukammer in einen Rahmen eingespannt oder in eine Form eingebettet. Anguss und Formtrennebene werden festgelegt. Dann wird Flüssigsilikon um den Prototypen gegossen und unter Vakuum erwärmt. Das Vakuum verhindert Lufteinschlüsse in Form und Werkstück und erhöht so die Präzision der Abgüsse. Nach dem Aushärten des Silikons wird die entstandene Silikonform in Übereinstimmung mit den Formtrennebenen auseinander geschnitten und der Prototyp bzw. das Urmodell entfernt.
Zum eigentlichen Vakuumgussverfahren: Nach dem Entformen des Prototyps kann die fertige Silikonform sofort für den Vakuumguss der zu fertigenden Kunststoffteile verwendet werden. Auch hierbei wird die Form im Vakuum mit flüssigem Rohmaterial – meist Zweikomponenten-Gießharze – befüllt und ggf. erwärmt. Nach Aushärten des Materials wird das Werkstück entfernt, im Wärmeschrank nachgehärtet und je nach Bedarf nachbearbeitet.
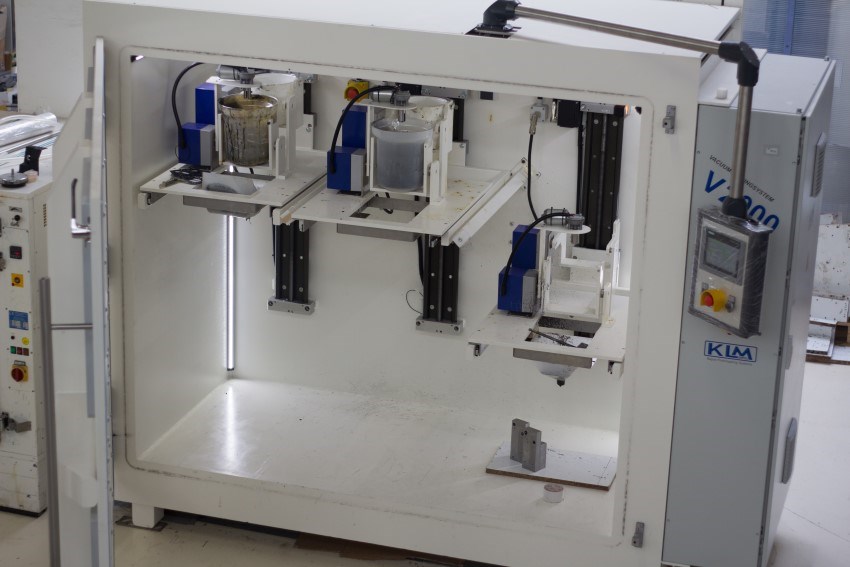
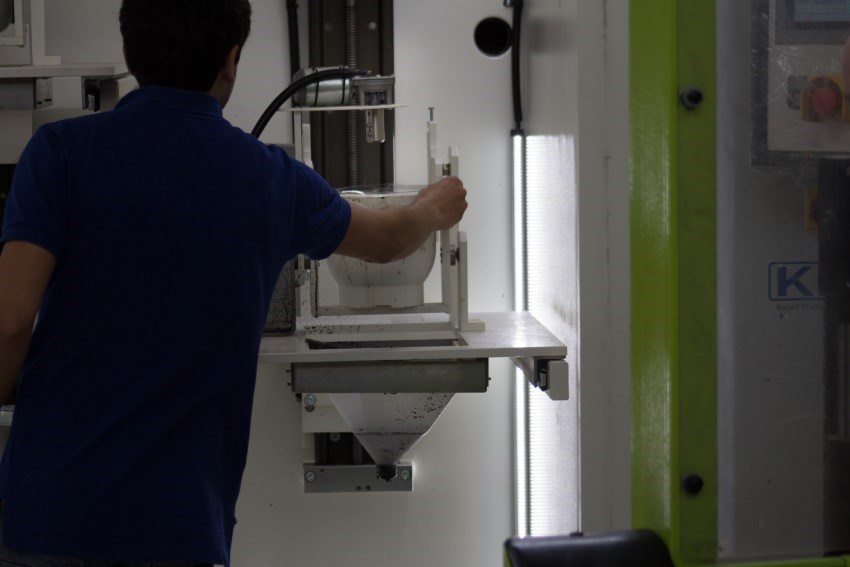
Wichtig: Die Maßhaltigkeit, Formgenauigkeit und Oberflächenqualität des Urmodells bestimmen dabei die Qualität der Silikonform und damit der Vakuumgussteile.
Die Werkstoffe: Feuerfest, lichtdurchlässig, lebensmittelecht – und mehr
Die Bandbreite der Materialeigenschaften vakuumgegossener Bau- und Formteile ist groß. So lassen sich je nach verwendetem Werkstoff mittels Vakuumguss flexible, gummiartige Dichtungen ebenso herstellen wie bruchfeste und schlagzähe Teile. Die Temperaturbeständigkeit variiert zwischen -50 und +200 Grad Celsius. Auch chemikalienbeständige Teile sind möglich. Eine Besonderheit bieten Diffusor-Werkstoffe, die Licht ideal streuen, so dass sich Bauteile realisieren lassen, die überall gleich durchscheinend sind. Manche Hersteller bieten auch lebensmittelechte Teile an.
Die am häufigsten eingesetzten Zwei- oder Mehrkomponenten-Gießharze – Polyurethane – bestehen dabei aus Kunstharz und Härter sowie je nach Bedarf weiterer Zusätze wie Farben, Füllstoffe, Verstärkungsmaterialien wie Glasfasern etc. Sie werden vermischt bei Raumtemperatur oder unter zusätzlicher Wärmezufuhr verarbeitet.
Darüber hinaus finden Elastomere (PU-Gummi) und niedrigschmelzende Metalllegierungen im Vakuumguss Verwendung. Eine Kombination verschiedener Materialien – zum Beispiel bei Hart-Weich-Teilen – durch einen mehrstufigen Fertigungsprozess oder die Herstellung von Teilen mit Metalleinlegern sind möglich.
Vakuumguss im Überblick:
Vorteile
- Preiswerte Herstellung von Formen und Bauteilen, u.a. deutlich günstiger als Kunststoffspritzguss
- Schnelles Verfahren mit einer Gesamtdauer von wenigen Tagen bis Wochen vom Prototypen zum vakuumgegossenen Formteil
- Hinterschnitte und nahtlose Hohlkörper (mit Ausschmelzkern) möglich
- Funktionsintegration durch die Einbindung von Norm- und Formteilen wie Lagerbuchsen oder Gewindebolzen in das Werkstück bereits während des Gussvorgangs möglich
- Kleinste Formen (Mikrospritzguss), aber auch große Teile herstellbar
- Sehr genaue Bauteile mit hoher Maßhaltigkeit und Oberflächenqualität realisierbar
- Leichte Entformbarkeit
- Beschleunigung des Fertigungsprozesses mit Hilfe von Mehrfachformen mit mehreren Kavitäten zur gleichzeitigen Fertigung von Werkstücken möglich
- Kombination verschiedener Materialien in einem Bauteil, z.B. Hart-Weich-Teile, oder Fertigung von Objekten mit Metalleinlegern durch Mehrschrittverfahren möglich
Nachteile
- Schneller Verschleiß der Formen, daher nur für Kleinserien geeignet
- Nur niedrigschmelzende Rohmaterialien verwendbar, da Silikonformen nur begrenzte Verarbeitungstemperaturen erlauben
- Verschlissene Formen problematisch in der Entsorgung
- Hohlkörper nur mit Auschmelzkern realisierbar
Sie haben bisher nur ein 3D-CAD-Modell, aber kein Urmodell? Gern vermitteln wir Ihnen ein Angebot für die generative Fertigung Ihres Produkts, ob mittels Stereolithographie oder traditionell gearbeitet. Sprechen Sie uns an. Wir finden eine Lösung.
Sie haben Fragen? Wir beanworten Sie gern. Kontaktieren Sie uns unter info@vioproto.de.
Kommentarbereich geschlossen.